Výroba a obrábění
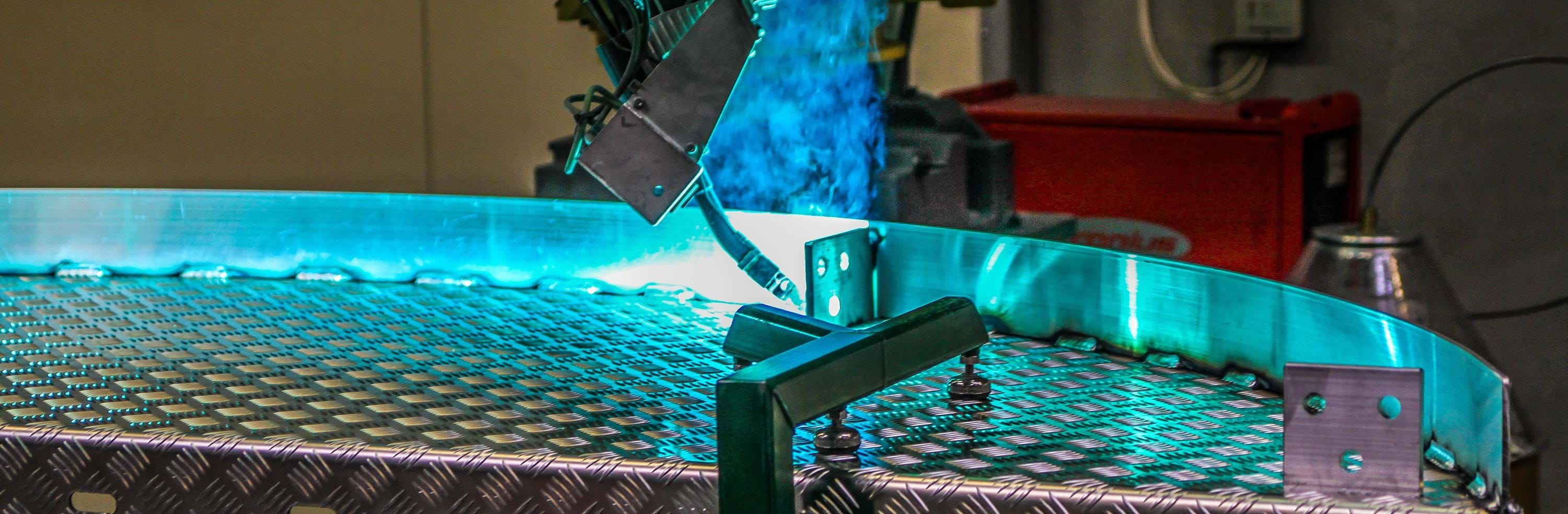
Aluminium can be fabricated and machined with a range of different methods for different purposes. The most common methods are machining, e.g. turning, milling and punching.
Aluminium is also suitable for welding – but you will need a basic understanding of the metal first.
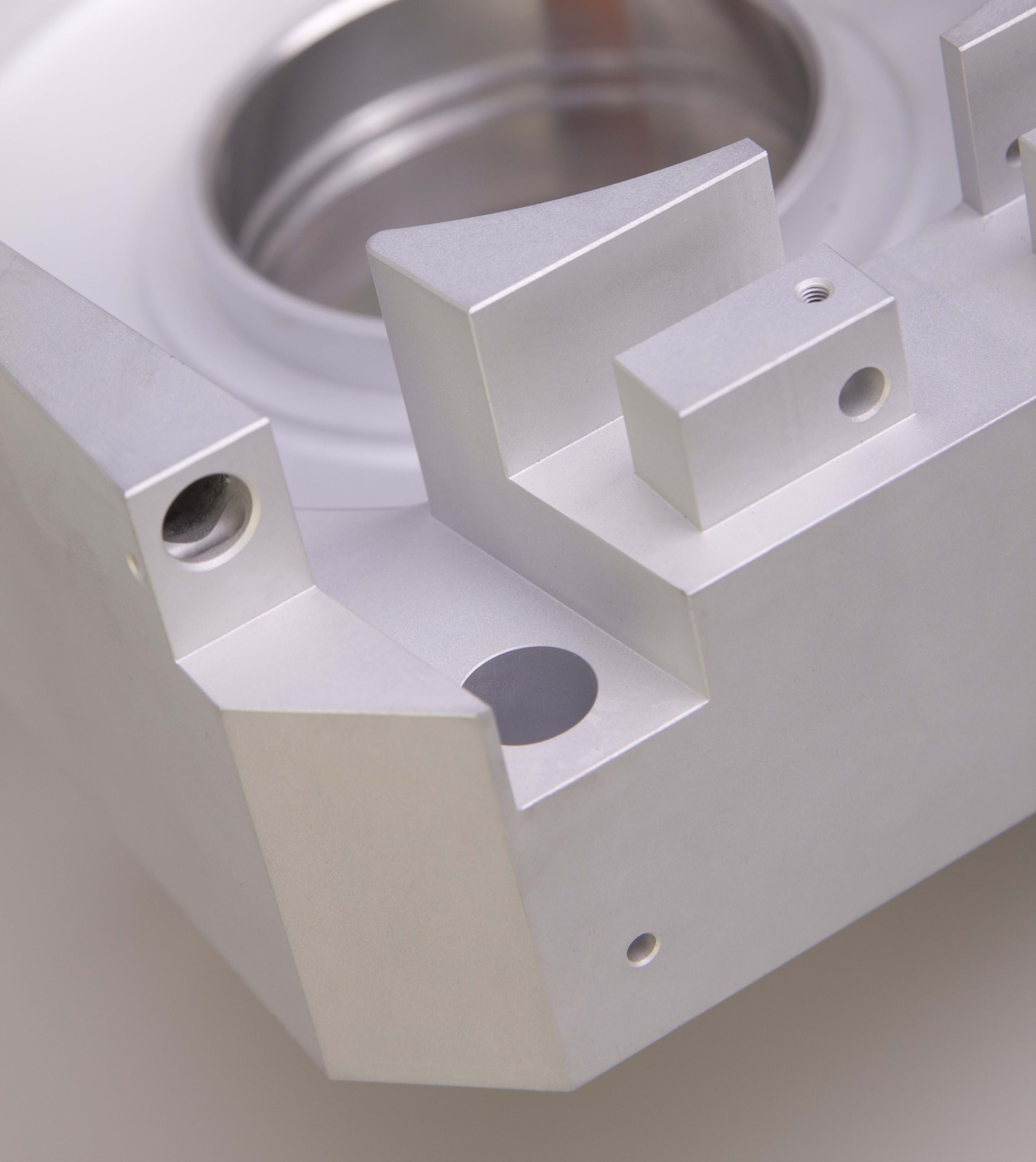
Some alloys are better suited for machining than others. Generally speaking, a hard alloy is better suited for machining because the chips are short and hard. A soft alloy produces long, soft chips that get in the way of machining and can get stuck in the machine.
Aluminium is a soft metal on its own, so an alloy with a relatively high content of other metals - preferably copper – is a good way to go.
Examples of hard alloys include: 2007, 2011, 5083, 6026, 6082, 6262R and the 7xxx series.
We can advise you on the best alloy with the right combination of properties for your project.
Turning and milling
Turning and milling are the most common types of machining, and they are usually done with a CNC machine. Typical examples would be milling holes in an extruded aluminium profile or turning complex parts like in this video:
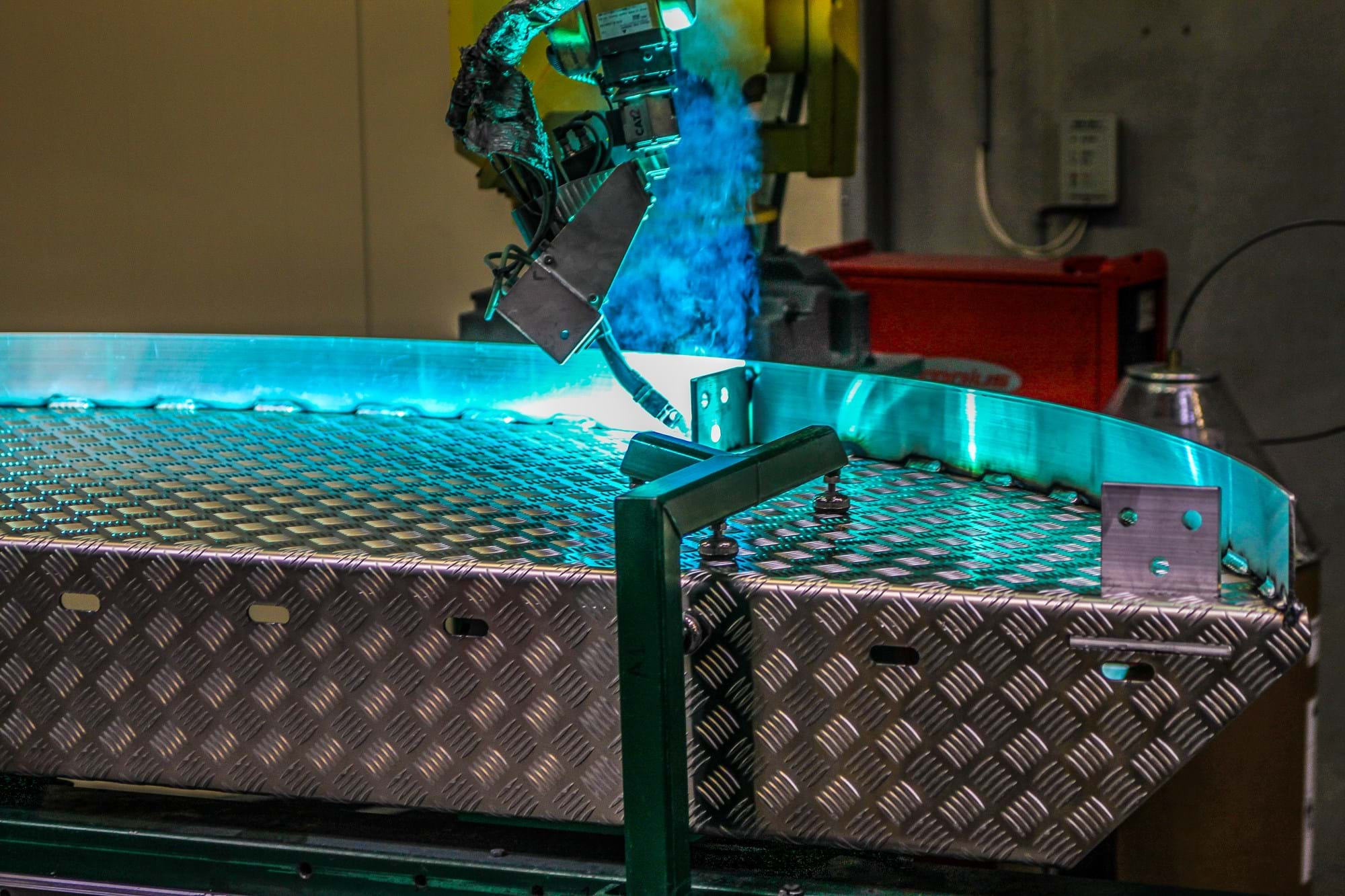
If you are used to welding steel, there are a few things you should be aware of before welding aluminium.
Firstly, aluminium reacts with oxygen and hydrogen from the surroundings during welding. Secondly, the heat from the welding spreads through aluminium much faster than with steel. But with a few precautions, you can weld aluminium without problems.
Aluminium forms an oxide layer
Raw aluminium instantly forms an oxide layer when it comes into contact with oxygen. The melting point of the oxide layer is 2060 °C, significantly higher than for the raw aluminium. This means that the oxide layer does not melt during welding, and the welding process even stimulates the formation of the oxide layer.
To get around this issue, you need to penetrate the oxide layer before and during welding. TIG and MIG welding are methods developed for this specific purpose.
Hydrogen can cause pores
Liquid aluminium absorbs hydrogen from the surrounding air. When the metal cools down, the hydrogen gas is released again. As the hydrogen leaves the welding seam, it can cause pores and weaken the material. To avoid this, use a welding method suited for aluminium.
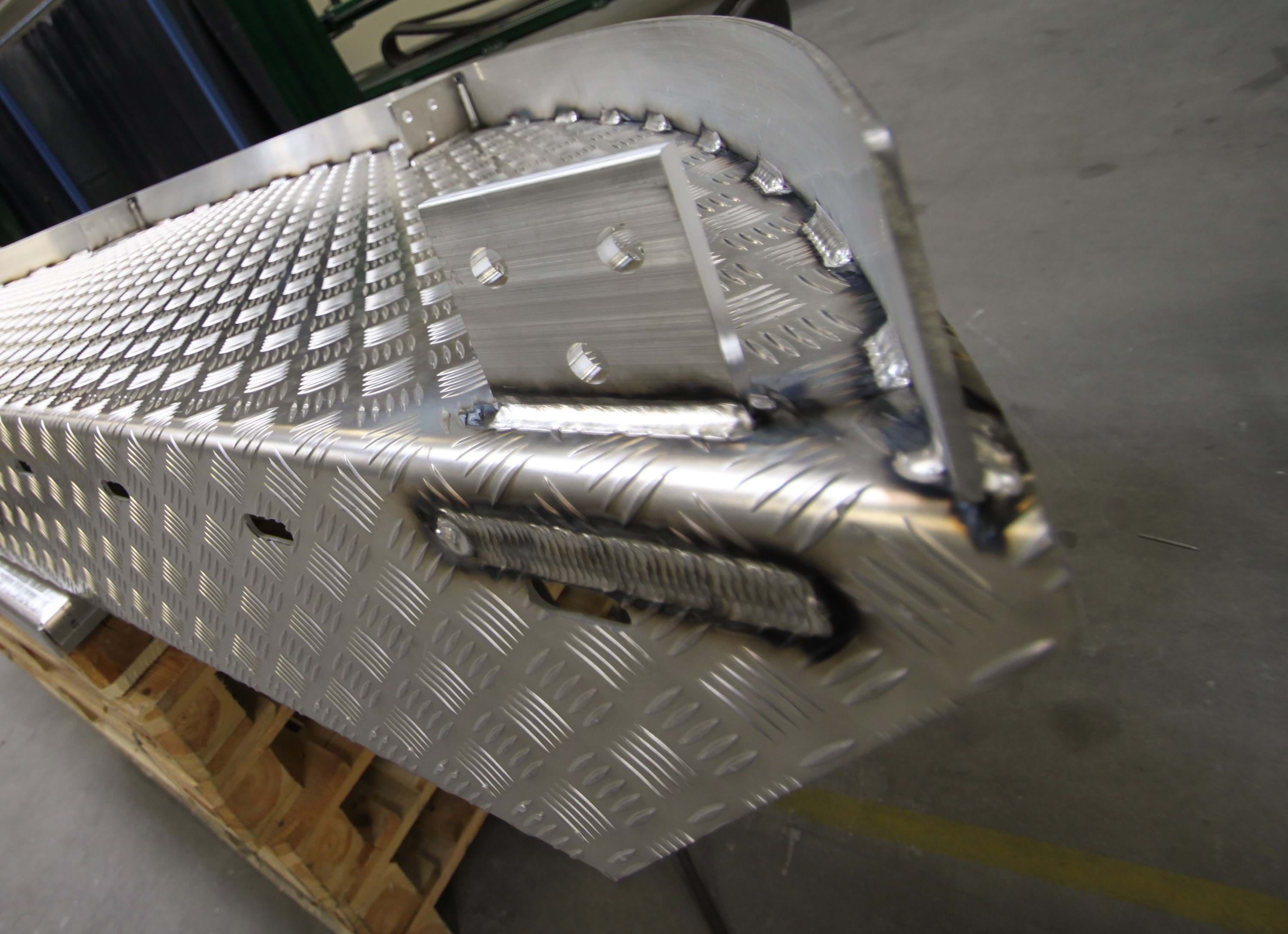
When welding aluminium, you need to account for the physical properties of the metal.
The melting point of aluminium is around 660 °C. This is low compared to other materials – steel has a melting point of 1500 °C.
But the thermal conductivity of aluminium is high, meaning that you need a large input of heat during welding.
The combination of a low melting point and high thermal conductivity means that there is a risk of overheating the metal – especially if you are used to steel welding.
HAZ – Heat Affected Zone
As a result of the high thermal conductivity, the HAZ (Heat Affected Zone) of aluminium is large.
It is important to consider the HAZ when welding, because the heat can permanently weaken the affected area. If the welded material is anodized before welding, the HAZ can become permanently discoloured.
As a rule of thumb, the HAZ is approximately 1 inch on each side of the welding seam. Refer to EN1999-1-1 for the expected weakening of the HAZ for a specific alloy.
We always recommend using certified welders and consult certified consultants about a specific welding project.
TIG and MIG welding
To avoid the possible issues with oxygen and hydrogen from the sorroundings during welding, a shielding gas is always used when welding aluminium. The most common methods for welding aluminium are TIG and MIG welding.
TIG stands for Tungsten Inert Gas and uses a tungsten electrode during welding.
TIG is a hand-held weld and is easy to control and clean. However, it requires a lot of heat, which, due to the heat density of aluminium, creates a large HAZ (Heat Affected Zone) and weakens the material.
MIG stands for Metal Inert Gas and is an automatic welding method. The method is significantly faster than TIG welding, but less precise. In addition to speed, the advantage of MIG welding is that it requires less heat and thus weakens the metal less than TIG welding does.
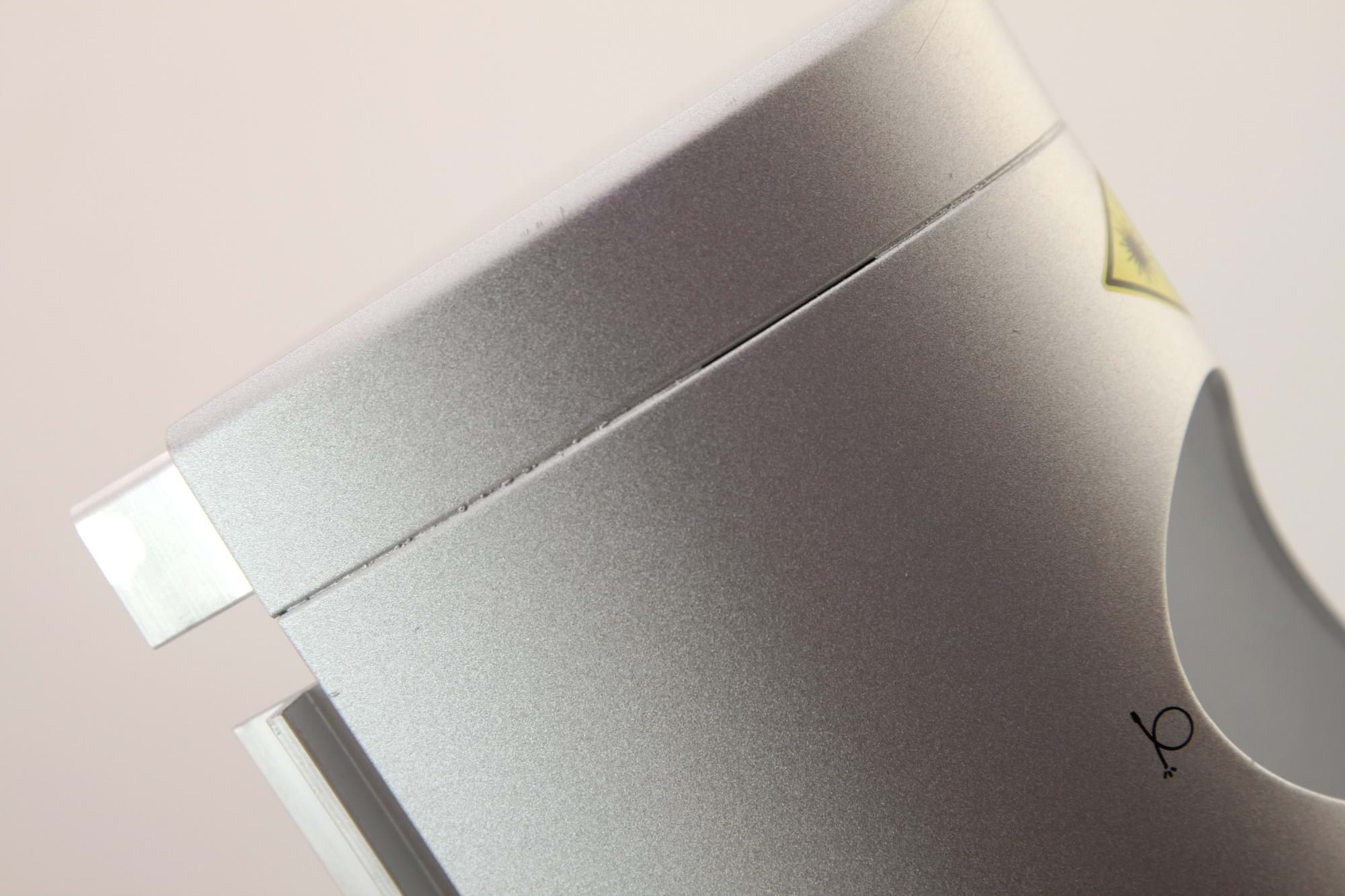
As an alternative to bolting or welding, aluminium parts can be bonded together with glue.
Glue weighs a lot less than bolts and screws, and there is no visible joint.
Unlike welding, bonding does not use heat on the metal. This eliminates the risk of heat-induced changes to the physical and chemical properties of the aluminium.
We always recommend seeking advice from the adhesive manufacturer to ensure the right choice of adhesive.
Laser cutting
Aluminium sheets can be laser cut for fast and efficient cutting. However, not all alloys are equally suitable for laser cutting: for example, an alloy such as 1050A can reflect the laser beam back into the laser head and damage the machine.
To avoid complications, we recommend seeking advice from the manufacturer of the laser cutter before laser cutting aluminium.
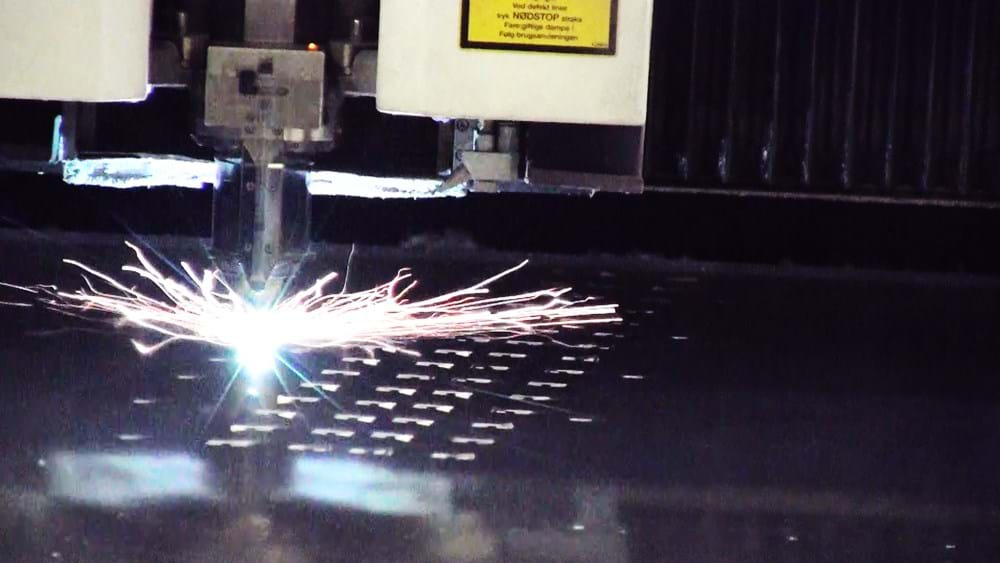